Whether you're working with aerospace components, automotive parts, or custom prototypes, the role of machining tolerances cannot be overstated. Tolerances are the backbone of successful design, ensuring that parts fit together and function correctly under real-world conditions. In this blog, we’ll explore tolerances, why they are essential, and how they impact manufacturing processes like CNC machining, injection molding, and more.
What Are Machining Tolerances?
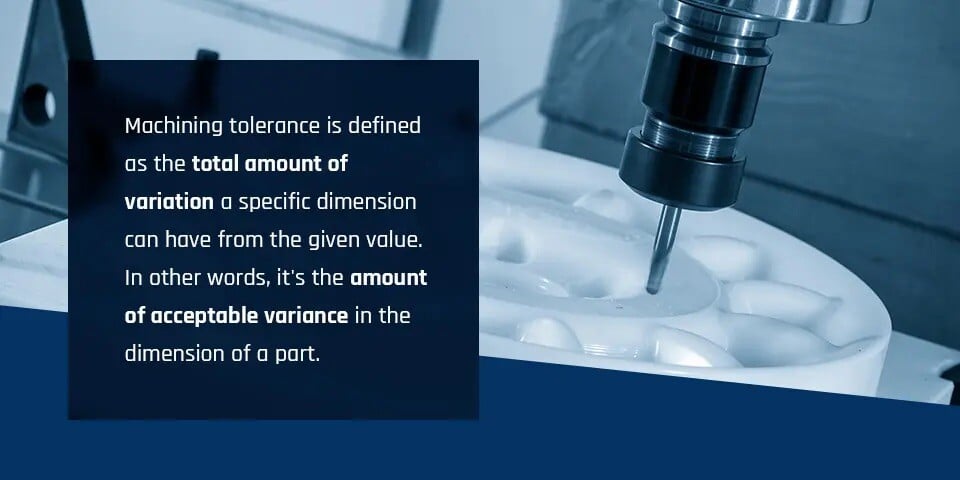
At its core, a machining tolerance is the permissible limit of variation in a physical dimension. When a part is designed, it is rarely practical (or necessary) for every feature to be manufactured to an exact dimension. Instead, a tolerance defines the allowable margin of error within which the part will still function as intended. For example, if the diameter of a shaft is specified as 50 mm, a tolerance might be +/- 0.1 mm, meaning the actual diameter can range between 49.9 mm and 50.1 mm and still be acceptable.
This slight deviation is critical because it accounts for variations in the manufacturing process, whether from tool wear, material properties, or machine capabilities. Machining tolerances ensure that parts can be produced efficiently without unnecessary waste or delays while maintaining their intended functionality.
Why Are Tolerances Important?
The significance of tolerances can’t be overstated. They impact cost, functionality, and manufacturability across various industries, especially in fields such as aerospace, automotive, and medical device manufacturing. Here are a few reasons why tolerances are crucial:
- Interchangeability of Parts: Tolerances ensure that parts manufactured in different locations or by different vendors fit together seamlessly. Eli Whitney famously pioneered this concept during the development of interchangeable parts for firearms in the early 19th century. Today, Geometric Dimensionaling and Tolerancing (GD&T) systems provide a standardized way to define tolerances, ensuring consistency across production lines.
- Cost Efficiency: Overly tight tolerances can drive up production costs by requiring specialized machinery, secondary operations like grinding or EDM, or extended inspection times. Conversely, too loose tolerances may result in defective parts, causing costly rework or failure in the field. Striking the right balance is key to minimizing production and quality control costs.
- Functionality and Performance: Tolerances directly influence a part's performance under operational conditions. In aerospace applications, for example, components often need to operate under extreme stress and temperature variations, making tight tolerances essential to ensure safety and reliability.
Types of Machining Tolerances
Understanding the different types of tolerances is essential for both designers and machinists. These tolerances dictate how dimensions are controlled during manufacturing:
- Linear Tolerances define acceptable variations in length, width, or height. For instance, in CNC machining, a typical standard might be +/—0.005 in. (0.13 mm) for production runs, though precision machining can achieve tolerances as tight as +/—0.0005 in. (0.0127 mm) for critical features.
- Geometric Tolerances: These cover features' shape, orientation, and position. GD&T standards like flatness, cylindricity, and perpendicularity are critical in ensuring parts perform as expected.
- Surface Finish Tolerances: Often overlooked, surface roughness is crucial in how parts fit together and operate under friction. Many parts require a smooth finish, which might necessitate additional post-processing steps like bead blasting or polishing to meet the required surface finish.
Tolerances in Different Manufacturing Processes
Tolerances vary across different manufacturing processes, each of which has its strengths and limitations:
- CNC Machining: CNC machining offers highly controlled tolerances, often as tight as +/- 0.002 in. for production parts. This process is ideal for precision parts, especially in industries like aerospace and defense, where accuracy is crucial.
- Injection Molding: In injection molding, tolerances depend largely on factors like material shrinkage and mold design. Due to the nature of the material flow and cooling process, injection-molded parts typically require a looser tolerance than machined parts. However, engineers can optimize the design to account for these tolerances.
- Sheet Metal Fabrication: Sheet metal parts are typically held to tolerances governed by the ISO 2768-1 standard, which defines acceptable deviations in flatness, angles, and radii. Manufacturers often aim for a balance between achieving tight tolerances and maintaining the cost-effectiveness of production.
Optimizing Tolerances for Cost and Performance
Balancing tight tolerances with cost is an ongoing challenge in engineering design. Tight tolerances lead to better performance and reliability, but they can also significantly drive up manufacturing costs, especially when specialized tooling or climate-controlled environments are required. A more relaxed tolerance can save time and money but at the risk of introducing quality issues or requiring post-production adjustments.
Engineers often rely on tolerance optimization techniques when designing for aerospace or automotive applications, where safety is a paramount concern. These techniques aim to minimize the total cost by balancing manufacturing cost, quality control, and performance degradation due to excess weight or material use.
In aircraft manufacturing, for example, selecting the right tolerance for a critical component like a fastener hole can distinguish between scrapping a part or completing it successfully within the defined inspection interval(conf110). This is particularly true for fatigue-critical components like wing spars, where minor deviations can significantly reduce the part’s lifespan.
Common Pitfalls and How to Avoid Them
One of the most common mistakes when applying tolerances is specifying tolerances that are tighter than necessary. This not only increases production costs but also complicates quality control. Conversely, loose tolerances can lead to problems during assembly, making it impossible for parts to fit together correctly.
To avoid these pitfalls, engineers should:
- Leverage Simulation Tools: Modern CAD software can simulate how tolerances will impact part performance, helping engineers find the optimal balance before production begins(Validating Tolerances -…).
- Use GD&T When Appropriate: Geometric Dimensioning and Tolerancing offers a standardized approach to controlling dimensions and relationships between part features, reducing the likelihood of miscommunication between designers and machinists.
- Work Closely with Manufacturers: Collaborating with manufacturers early in the design process can help avoid overly tight tolerances that drive up costs or cause delays.
Conclusion: The Importance of Tolerances in Manufacturing
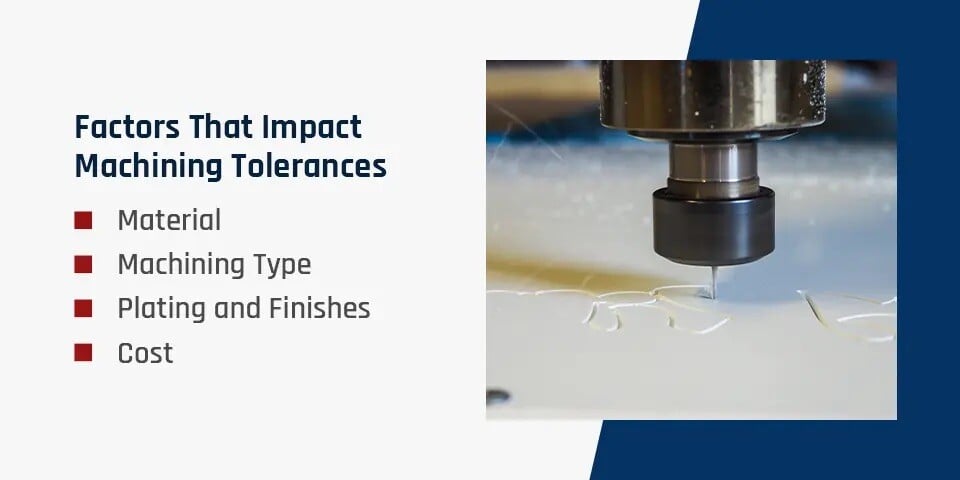
Machining tolerances are pivotal in modern manufacturing, ensuring that parts are produced efficiently, function correctly, and meet performance standards. Whether you are designing a part for aerospace, automotive, or consumer products, understanding and applying the right tolerances is critical to achieving success.
By carefully balancing the need for precision with the realities of manufacturing costs, engineers can design parts that are not only functional but also cost-effective. CADmore provides expert design and engineering services, working with clients across industries to ensure their parts are manufactured to the highest standards while keeping production costs in check.
Contact us today for more information on how CADmore can assist with your CNC machining, tolerance optimization, and product development needs.