Metal Injection Molding (MIM) is a manufacturing process that combines the versatility of plastic injection molding with the strength and durability of metal. MIM is widely regarded as one of the most efficient and cost-effective ways to produce complex, high-strength metal parts at high volumes. By leveraging the benefits of powder metallurgy and plastic molding, MIM provides a method for creating small, detailed components that would be difficult or costly to produce using other techniques.
The Metal Injection Molding Process: How It Works
MIM begins with creating a feedstock composed of fine metal powders mixed with a binder. This binder, which contains plastic materials, allows the metal powder to be injection molded, similarly to plastic injection molding processes. The process involves the following steps:
- Feedstock Preparation: Metal powders are mixed with thermoplastic binders to create a homogeneous feedstock. The binder serves as a temporary vehicle, making the metal powder moldable. The feedstock must be carefully prepared to ensure the right consistency and viscosity for injection molding.
- Injection Molding: The prepared feedstock is injected into a mold cavity under high pressure. This is similar to traditional plastic injection molding, and allows the formation of intricate, complex geometries. Once injected, the resulting part, known as the "green part," has the desired shape but lacks the final material properties.
- Debinding: During this step, the binders used in the feedstock are removed from the "green part." The removal can be achieved through a combination of solvent extraction, thermal processing, or catalytic methods. This process transforms the green part into a porous structure known as the "brown part."
- Sintering: The brown part is heated to a temperature just below the melting point of the metal, usually in a controlled atmosphere. During sintering, the metal particles bond together, densifying the component and shrinking it to its final size. This step is crucial as it provides the strength and mechanical properties equivalent to forged or wrought parts. The sintering process can shrink the component by 15-20%, which must be accounted for in the mold design.
- Post-Processing: Depending on the application, post-sintering processes, such as machining, heat treatment, or coating, may be performed to enhance the part's characteristics. For example, plating or heat treatments like carburizing or nitriding can be applied to further enhance surface properties.
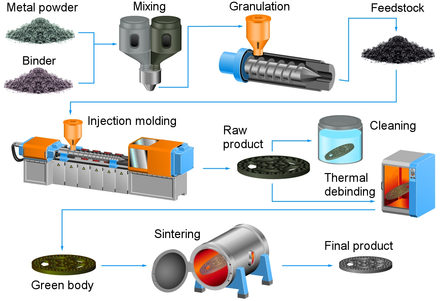
Materials Used in MIM
MIM is compatible with a wide variety of metals, allowing for significant material flexibility. Common materials used include:
- Stainless Steels: Such as 316L, 17-4 PH, and 420P, which provide corrosion resistance and strength, suitable for medical and consumer applications.
- Low-Alloy Steels: Often used in automotive and industrial applications due to their balance of machinability and strength.
- Tool Steels: Including M2, known for their hardness and wear resistance, ideal for tools and cutting applications.
- Tungsten and Cobalt Alloys: Utilized for components requiring high density or specific electromagnetic properties, such as shielding applications in aerospace or medical devices.
Key Benefits of Metal Injection Molding
- Complex Geometries: MIM allows for the creation of highly intricate and complex shapes that would be difficult or impossible to achieve using traditional manufacturing methods. Features like undercuts, overhangs, internal threads, and thin walls are possible with MIM, making it ideal for producing parts with high design complexity.
- Material Efficiency: Compared to traditional machining, which removes material from a solid block, MIM significantly reduces waste by forming parts directly to near net shape. This is particularly beneficial for expensive materials, where minimizing scrap is crucial for cost efficiency.
- High Production Volume: MIM is designed for mass production. Once the mold is created, MIM can produce thousands of identical parts with high repeatability and minimal variation. This is one of the reasons why MIM is a cost-effective solution for high-volume manufacturing.
- Superior Mechanical Properties: Parts produced via MIM have mechanical properties that are comparable to those produced using more conventional metalworking techniques, such as casting or forging. The sintering process ensures that the final component is nearly fully dense, often reaching densities of 96-99%, which imparts excellent strength and durability.
- Reduced Secondary Operations: Since MIM produces parts close to their final shape, there is often little to no need for secondary operations like machining. This leads to lower production costs and shorter lead times.
Applications of Metal Injection Molding
MIM is utilized across various industries, especially for producing small parts that require complex geometries. Here are some examples:
- Automotive Industry: Parts such as gear synchronizers, fuel injector components, and locking mechanisms can be efficiently manufactured through MIM. The precision and strength of MIM parts make them ideal for these demanding applications.
- Medical Devices: MIM is widely used for surgical instruments, endoscopic devices, and implantable components. Stainless steel alloys processed via MIM offer biocompatibility and high precision, critical for medical applications.
- Firearms: The MIM process is heavily used in the firearms industry for components such as triggers, safety levers, and other intricate mechanisms where consistency and strength are paramount.
- Consumer Electronics: MIM produces miniature components like connectors, structural parts for smart devices, and housings. Creating highly detailed parts without costly secondary processing is a major advantage for consumer electronics.
- Aerospace: The aerospace sector benefits from MIM through parts like turbine blades, fuel system components, and structural supports. These parts require high precision, lightweight designs, and the ability to withstand high stresses and temperatures, all of which MIM can provide.
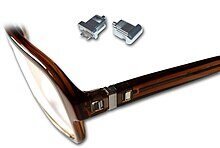
Challenges and Considerations in MIM
- High Start-Up Costs: The initial investment in molds and equipment is significant, which makes MIM most suitable for large production runs. The cost of tooling and setup needs to be spread across many units to be economically viable.
- Shrinkage Control: During the sintering process, MIM parts shrink significantly (15-20%). This shrinkage must be precisely controlled, and adjustments must be made during mold design to ensure the final product meets the required dimensions. While manufacturers typically handle these calculations, it is an important factor in the design process.
- Size Limitations: MIM is typically used for smaller parts (usually under 100 grams), as larger parts can lead to challenges in maintaining consistency and controlling shrinkage. Additionally, the cost of sintering larger parts may not be practical for most applications.
Design Guidelines for MIM
- Uniform Wall Thickness: Maintaining uniform wall thickness reduces the risk of defects such as warpages during sintering. This guideline helps achieve better flow during injection molding and consistent densification during sintering.
- Complex Features: MIM can accommodate features like external threads, holes, and overhangs without requiring additional processing. However, designers should aim for gradual transitions and avoid sharp corners to minimize stress concentrations during sintering.
- Draft and Ejection: Incorporating draft angles helps in the easy ejection of parts from the mold, reducing wear and improving the lifespan of the tooling.
Conclusion
Metal Injection Molding (MIM) is a robust manufacturing process that blends the advantages of powder metallurgy and plastic injection molding to produce complex, high-strength metal components efficiently. It excels in creating intricate geometries with excellent mechanical properties, making it suitable for various industries, from automotive to medical. While initial costs are associated with tooling and setup, the benefits of reduced material waste, high production volumes, and the ability to create near-net shapes make MIM an attractive solution for producing precision metal parts.
If you're looking for an efficient way to manufacture small, complex metal components, MIM might be the right choice for your application. CADmore offers a range of 3D design and engineering services, including expertise in MIM, to help take your product from concept to high-volume production. Contact us to learn more about how we can assist with your next project.