When it comes to manufacturing metal parts, engineers and manufacturers face a crucial choice: Metal Injection Molding (MIM) or Metal Additive Manufacturing (Metal 3D Printing)? Both processes offer unique advantages and challenges, depending on the specific application, complexity, and production volume of the component. In this article, we delve into a detailed comparison between MIM and metal 3D printing, highlighting key considerations such as cost, design flexibility, production speed, and volume requirements to help you make an informed decision.
What is Metal Injection Molding (MIM)?
Metal Injection Molding combines the precision of plastic injection molding with the strength of metal powders, allowing manufacturers to create small, intricate metal parts with high tolerances. The MIM process includes four main steps:
- Feedstock Preparation: Metal powders are mixed with a binder to create a moldable feedstock.
- Injection Molding: The feedstock is injected into a mold to create a "green part."
- Debinding: Most of the binder is removed, resulting in a "brown part."
- Sintering: The brown part is sintered at a high temperature to achieve its final properties, with up to 95-98% density.
MIM is best suited for high-volume production of small parts that require tight tolerances and consistent quality. It is widely used in industries like medical devices, automotive, aerospace, and consumer electronics, where production stability is critical.
What is Metal 3D Printing?
Metal Additive Manufacturing (Metal 3D Printing) involves creating parts layer by layer from metal powders, using technologies such as Binder Jetting, Selective Laser Melting (SLM), or Direct Metal Laser Sintering (DMLS). Metal 3D printing offers unmatched design flexibility and is ideal for creating complex geometries without the constraints of traditional tooling.
Metal 3D printing is used extensively for prototyping, low-volume production, and customized parts. Unlike MIM, 3D printing doesn’t require molds, which allows for rapid design iteration and significant cost savings when producing complex or changing parts.
Key Considerations: MIM vs Metal 3D Printing
1. Production Volume
- High Volume: MIM is the preferred choice when producing parts in large quantities, typically over 20,000 units annually. The cost of molds in MIM ($5,000 to $100,000) is amortized over large volumes, making it cost-effective for long-term production.
- Low to Mid Volume: Metal 3D printing becomes more economical for low to mid-volume production. Without the need for costly molds, manufacturers can produce fewer parts while keeping costs low. Technologies like Binder Jetting also make high-volume 3D printing more feasible by reducing production costs compared to other additive methods.
2. Lead Times
- MIM Lead Times: MIM has a longer lead time due to the need for tooling. Designing and manufacturing molds can take 8 to 20 weeks before full-scale production can begin.
- 3D Printing Lead Times: Metal 3D printing significantly reduces lead times. Components can be printed directly from a digital file, allowing for a few days to weeks from design to production, especially for prototyping and low-volume applications.
3. Design Complexity
- Design Limitations in MIM: The MIM process involves the use of molds, which impose design limitations such as the avoidance of large overhangs and the necessity of uniform wall thicknesses. These constraints make it challenging to create highly complex geometries.
- Unlimited Design Freedom in 3D Printing: Metal 3D printing excels in producing parts with complex geometries, including internal structures, lattice designs, and custom features that are impossible to mold. The ability to make design changes on the fly is a significant advantage, as it involves only modifying a digital model rather than investing in a new mold.
4. Cost Considerations
- MIM Costs: MIM involves substantial tooling costs. While this cost can be justified for high-volume production, it is prohibitive for small runs. MIM also requires dedicated equipment for debinding and sintering, further adding to the cost.
- 3D Printing Costs: Metal 3D printing has a higher cost per part compared to MIM, especially for powder bed fusion technologies. However, new bind & sinter technologies like Binder Jetting have reduced the cost per part, making metal 3D printing competitive with MIM for certain production volumes.
5. Material Options and Properties
- MIM Material Options: MIM is compatible with a wide range of materials, including stainless steel, steel alloys, tungsten alloys, and ceramics. The sintering process results in parts with high density and strength, comparable to parts made through traditional metalworking methods.
- 3D Printing Material Flexibility: Metal 3D printing offers a variety of materials, including titanium, aluminum, and even precious metals like gold and platinum. The flexibility in material choice makes metal 3D printing suitable for specialized applications, such as medical implants and aerospace components, where specific material properties are critical.
6. Post-Processing
- MIM Post-Processing: After sintering, most MIM parts are ready for use without additional finishing. However, in some cases, secondary processes are needed to achieve tighter tolerances or a smoother finish.
- 3D Printing Post-Processing: Metal 3D printed parts typically require post-processing, such as heat treatment, stress relief, and surface finishing. These steps are essential to improve mechanical properties and achieve the desired finish, but they add to the overall cost and production time.
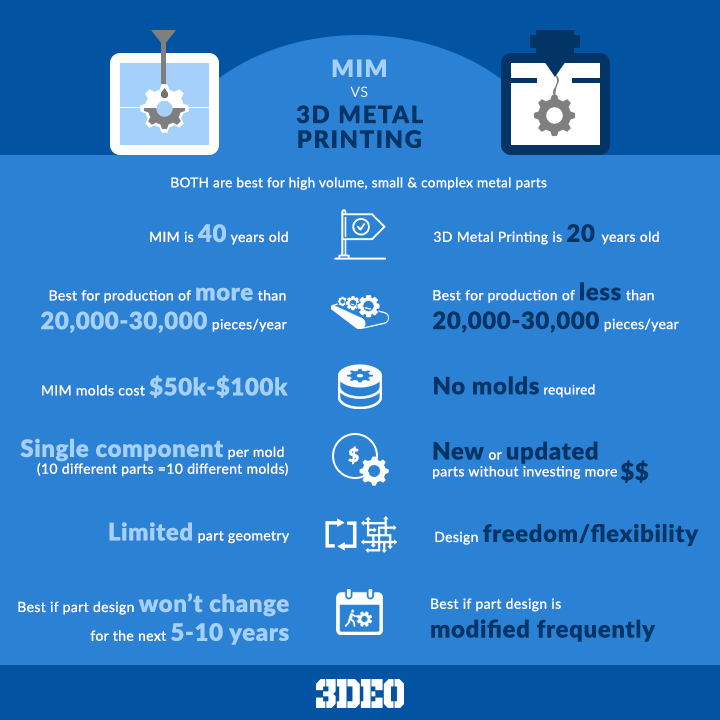
When Should You Choose MIM or Metal 3D Printing?
- Choose MIM if you need to produce small, high-volume parts with consistent quality and tight tolerances. MIM is ideal for projects where production stability, low unit cost, and long-term consistency are essential. This method is often used in automotive, medical, and consumer electronics industries, where parts must meet stringent quality standards at a reasonable cost.
- Choose Metal 3D Printing if you need low to mid-volume production, rapid prototyping, or parts with complex geometries. Metal 3D printing is suitable for applications where design iteration and flexibility are critical, such as custom medical devices, prototyping for aerospace, or specialized tooling. The ability to update designs without investing in new molds makes it an attractive choice for innovative and evolving projects.
Conclusion: The Best of Both Worlds?
Metal Injection Molding and Metal 3D Printing are both powerful manufacturing tools, each suited for different needs. MIM offers cost efficiency for high-volume, consistent production, while metal 3D printing provides unmatched flexibility for prototyping and custom parts. For many manufacturers, the best approach may be a combination of both—leveraging 3D printing for prototyping and tooling and transitioning to MIM for full-scale production.
Whether you're looking to optimize your product design, reduce costs, or speed up time-to-market, understanding the strengths and limitations of each technology can help you make the right decision for your project. If you’re still unsure which technology is best for your part, consider working with a trusted partner like CADmore, who can guide you through the process of choosing the right method for your specific requirements.