Metal Injection Molding (MIM) is an increasingly popular method for manufacturing complex metal parts with tight tolerances and high precision. This advanced process blends the flexibility of plastic injection molding with the mechanical properties of metal, making it ideal for applications across industries like automotive, medical, aerospace, and consumer goods. In this guide, we'll discuss how to design components specifically for MIM, highlighting best practices, common pitfalls, and optimization strategies for successful results.
Understanding the MIM Process
MIM involves several steps: mixing fine metal powders with a binder to create a feedstock, injecting the mixture into a mold, debinding, and sintering the molded "green parts" at high temperatures to achieve full density. Due to these unique steps, designing for MIM has its own set of considerations to ensure parts are both functional and manufacturable.
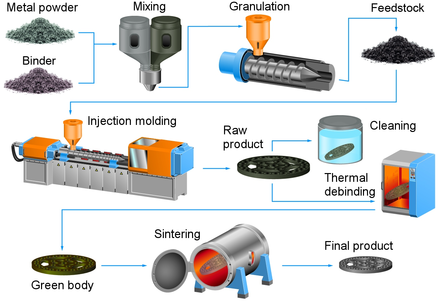
Key Design Considerations for Metal Injection Molding
To ensure that your design takes full advantage of the MIM process, it’s important to consider certain best practices and design constraints:
1. Wall Thickness
- Uniformity Is Key: Maintaining a uniform wall thickness is crucial in MIM to ensure uniform shrinkage and minimize warping during sintering. Recommended wall thickness ranges between 1 mm to 6 mm depending on the overall size of the part, with a preference for keeping the thickness consistent wherever possible.
- Avoid Thick Sections: Avoid sections thicker than 12.5 mm (0.5 inches) as they can lead to non-uniform shrinkage and increased sintering times. If a part requires thick sections, core them out to maintain a balance.
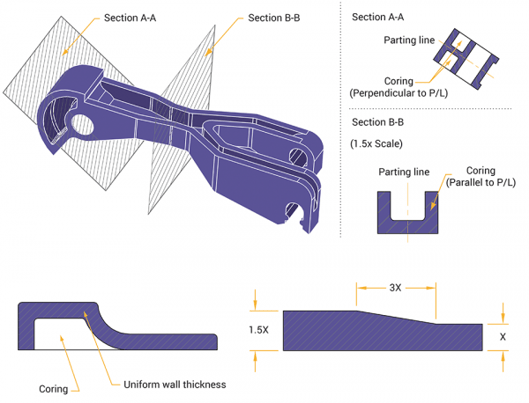
2. Parting Lines and Ejector Pins
- Minimize Visibility: Every MIM part will have parting lines where the two halves of the mold come together. Where possible, design parting lines on non-functional surfaces or less visible areas to minimize aesthetic and functional issues.
- Ejector Pins Consideration: All molded parts need to be ejected from the mold, which leaves ejector marks. It's recommended to position ejector pins in non-functional areas or use sleeve ejection methods to minimize marks altogether.
3. Draft Angles
- Limited Use in MIM: Unlike plastic injection molding, draft angles are often not necessary for MIM parts due to the use of wax as a mold release agent. However, in some situations, like when high aspect ratios are involved, a small draft of 0.5° to 2° may be beneficial.
4. Surface Features: Fillets and Radii
- Adding Fillets: Sharp corners are a no-go in MIM as they cause stress concentrations and can lead to defects. Adding fillets and radii of 0.4–0.8 mm helps to reduce stress during molding and sintering, improves material flow, and prevents premature part failure.
- Integration of Decorative Features: MIM allows for the easy integration of logos, part numbers, or other aesthetic features without adding extra costs. These features can be molded in as raised or recessed, ensuring clear identification and branding.
5. Gating and Flow Considerations
- Gate Positioning: The position of the gate (where the molten feedstock is injected into the mold) is vital for proper material flow. It is advisable to place the gate at the thickest section to promote balanced flow and minimize issues such as voids or sink marks. Locating gates on parting lines can also help reduce flow path disruptions.
- Multiple Gates for Complex Parts: Depending on the part's geometry, multiple gates may be required to ensure uniform filling and avoid material defects, particularly in larger or more complex designs.
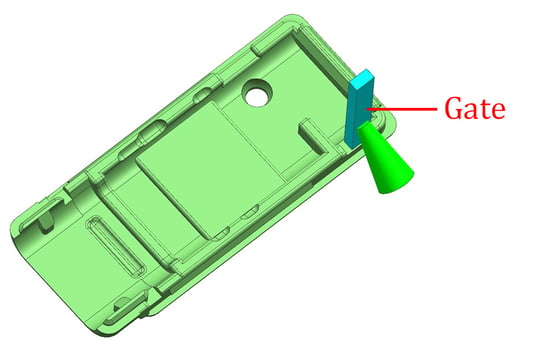
6. Holes, Slots, and Undercuts
- Designing Holes and Slots: Holes and slots are common in MIM components for reducing weight and improving functionality. They should be designed perpendicular to the parting line to facilitate easy molding. Coring holes, especially those with a high length-to-diameter ratio, helps reduce material usage and improve part stability during sintering.
- Undercuts and Threads: MIM allows for the molding of undercuts using collapsible cores, which is a unique advantage over other metal-forming techniques. Threads can also be molded directly, reducing the need for secondary machining.
7. Sintering Effects: Drag and Sag
- Account for Shrinkage: During sintering, MIM parts shrink by approximately 15-20%, and this shrinkage must be accounted for in the mold design. Proper design compensates for shrinkage to achieve desired part dimensions post-sintering.
- Preventing Sag: Unsupported features may sag during sintering due to gravity. Designing supports or incorporating gussets in areas prone to sagging can help mitigate this issue and maintain the integrity of complex geometries
Design for Manufacturing (DFM) in MIM
The concept of Design for Manufacturing (DFM) is critical in MIM to reduce production costs and eliminate the need for secondary operations. Key DFM principles in MIM include:
- Eliminating Secondary Operations: By designing features like knurls, logos, and part numbers directly into the mold, additional post-processing steps can be eliminated, reducing costs and lead times.
- Optimizing Part Complexity: MIM excels when producing parts that would otherwise require multiple components to be assembled. Combining these into a single MIM part reduces assembly time and increases the overall strength and reliability of the component.
Material Selection for MIM
Material selection in MIM plays a crucial role in determining the component's performance. Common materials include stainless steel, tool steel, and low-alloy steel, which provide high-density, corrosion resistance, and excellent mechanical properties.
- Ferrous Alloys: These are the most commonly used materials in MIM, ideal for applications requiring wear resistance and strength. For example, 17-4PH stainless steel offers good corrosion resistance, while tool steels provide high hardness for applications such as cutting tools and mold tools.
- Non-Ferrous and Special Alloys: Tungsten, titanium, and molybdenum alloys are also compatible with MIM and are used in specialized applications such as medical devices and aerospace components where high strength-to-weight ratios are required.
Common Pitfalls to Avoid in MIM Design
- Ignoring Wall Thickness Limitations: Designing with excessively thick or thin walls can lead to inconsistencies during sintering, including sinks, cracks, and warping.
- Overlooking Draft Angles and Parting Line Placement: While MIM doesn’t always require draft angles, overlooking parting line placement can result in visible imperfections, affecting both functionality and aesthetics.
- Neglecting Shrinkage Compensation: Failing to account for the 15-20% shrinkage during sintering can lead to parts that do not meet specification. Always consult with MIM specialists to determine the appropriate compensation measures.
Conclusion
Designing for Metal Injection Molding involves careful consideration of material flow, shrinkage, wall thickness, and part geometry to ensure both manufacturability and functionality. MIM offers numerous advantages for producing intricate, high-volume metal parts with fewer secondary operations, but it requires adherence to specific design guidelines for the best results.
By following these best practices—maintaining uniform wall thickness, considering gating and parting line placement, and accounting for sintering shrinkage—engineers can leverage MIM to produce highly complex and durable components efficiently. Remember, the best MIM parts are those designed with both performance and process in mind.
If you're considering using MIM for your next project, contact CADmore’s experienced engineers. We are here to assist with everything from concept design to full-scale production, ensuring your parts are optimized for the MIM process and ready to perform in demanding applications.