Die casting is a highly efficient manufacturing process to produce precise, complex metal parts at scale. In this advanced guide, we will explore the intricacies of die casting, covering how the process works, the materials used, its advantages, and key applications across industries.
Die Casting
Die casting is a metal casting process that involves forcing molten metal into a mold cavity under high pressure to create metal components with precise dimensions. The mold, known as a die, is typically made of steel and designed to withstand the high pressures and temperatures in the casting process.
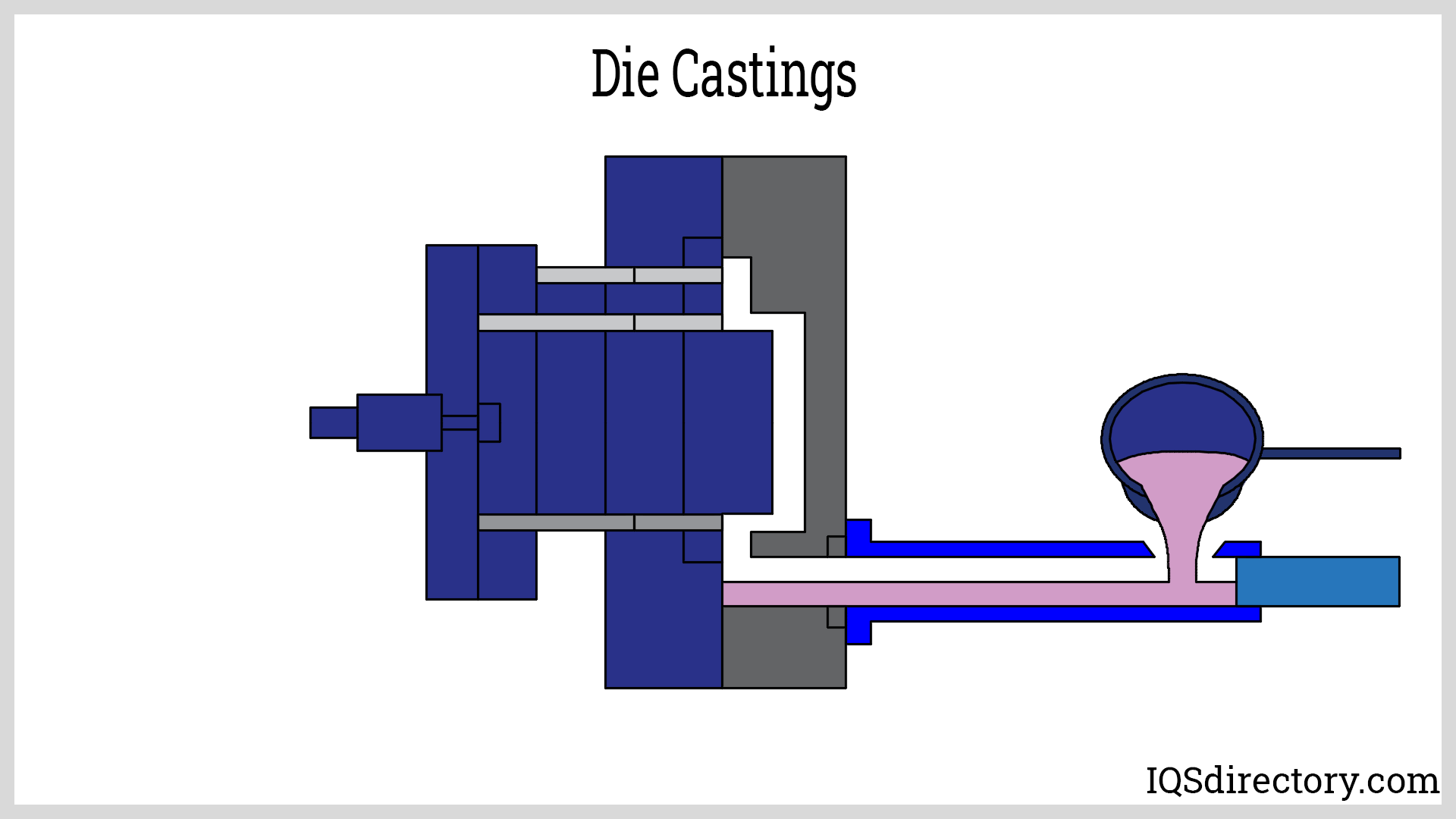
Die casting is widely used for producing complex metal parts with high dimensional accuracy and excellent surface finishes. This process can be divided into two main types: hot-chamber die casting and cold-chamber die casting.
Types of Die Casting Processes
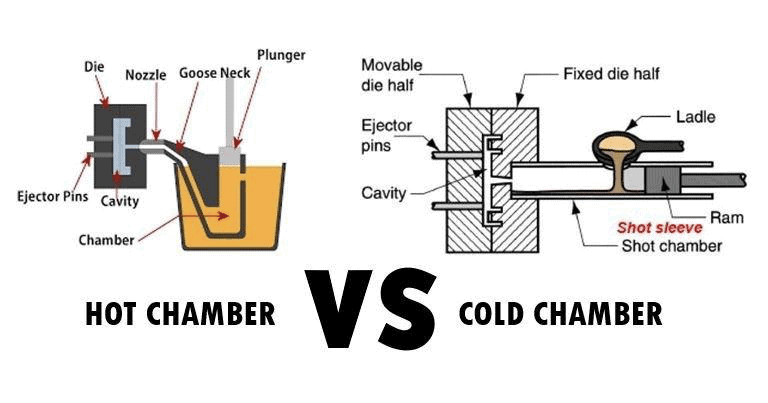
1. Hot-Chamber Die Casting
In hot-chamber die casting, molten metal is contained within the casting machine and injected into the die. This method best suits metals with low melting points, such as zinc, tin, and magnesium. Due to its built-in furnace system, hot-chamber die casting allows for rapid production but is unsuitable for higher-melting-point metals like aluminum.
2. Cold-Chamber Die Casting
Cold-chamber die casting is used for metals with higher melting points, such as aluminum, magnesium, and copper alloys. In this method, the molten metal is ladled into a cold shot chamber before being injected into the die at high pressure. Cold-chamber systems are ideal for materials that would otherwise damage the hot chamber’s built-in furnace.
Die Casting Materials
Choosing the right material is essential for achieving optimal results in die casting. The most commonly used die-casting metals are non-ferrous alloys, each offering specific benefits based on the application:
1. Aluminum
Aluminum is one of the most popular metals in die casting due to its high strength-to-weight ratio, excellent corrosion resistance, and ability to withstand high temperatures. It is frequently used in automotive, aerospace, and electronics industries. Aluminum die-cast parts are lightweight yet durable, making them ideal for applications requiring high performance without adding excess weight.
2. Zinc
Zinc alloys are known for their excellent fluidity and casting properties, making them perfect for complex shapes and thin-walled components. Due to its affordability and rapid cycle times, zinc die-casting is commonly used in consumer electronics, automotive parts, and electrical components.
3. Magnesium
Magnesium, the lightest of all structural metals, offers an excellent strength-to-weight ratio and is widely used in the automotive and aerospace industries. Magnesium die casting is preferred for parts that require weight reduction without sacrificing strength.
The Die Casting Process: Step-by-Step
The die casting process involves several key steps, each essential to producing high-quality, precision metal parts:
1. Mold Design
The process begins with the design of the mold, or die, which must withstand high pressures and temperatures. Molds are usually created from hardened steel and designed with great precision using CAD (computer-aided design) software. Dies are typically built in two sections to allow for the easy ejection of the cast part.
2. Metal Preparation
Once the mold is ready, the metal is melted to its liquid state in a furnace. The choice of metal will depend on the application, whether it’s aluminum, zinc, or magnesium.
3. Injection
The molten metal is then injected into the die at high pressure, filling the mold cavity completely. The high pressure ensures that the metal reaches all areas of the mold, creating detailed parts with tight tolerances.
4. Cooling
After injection, the metal is left to cool and solidify in the die. The cooling process ensures that the part maintains its precise shape.
5. Ejection and Trimming
Once the part has solidified, the die is opened, and the part is ejected. Excess material like flash is trimmed away to create the final product.
Advantages of Die Casting
Die casting offers several advantages over other manufacturing processes, including:
- High Precision and Dimensional Accuracy: Die casting can produce complex shapes with tight tolerances, making it ideal for industries requiring highly accurate components.
- Fast Production Rates: The die casting process allows rapid production, especially in high-volume runs. The quick cycle times reduce overall manufacturing costs.
- Excellent Surface Finishes: Parts produced through die casting often require minimal post-processing due to the smooth surfaces achieved during casting.
- Material Efficiency: Die casting minimizes material waste, making it an environmentally friendly option for producing metal parts.
Applications of Die Casting
Die casting is a versatile process used across a wide range of industries:
- Automotive: Die casting is widely used in the automotive industry for components like engine blocks, transmission housings, and gearboxes. Large-scale die casting machines like Tesla’s Gigapress create significant parts of the vehicle chassis, reducing weight and manufacturing complexity.
- Aerospace: The aerospace sector uses die casting to produce lightweight components with high strength and thermal stability, such as airframe parts and engine components.
- Electronics: Die-cast components, such as housings and connectors, are commonly used in electronic devices due to their excellent electromagnetic shielding properties.
- Consumer Products: From everyday kitchen appliances to high-tech gadgets, die casting creates durable, aesthetically pleasing parts that can withstand wear and tear.
Conclusion: Why Choose Die Casting for Your Project?
Die casting offers unmatched precision, speed, and material efficiency for producing metal parts at scale. Whether you're in the automotive, aerospace, or electronics industry, die casting provides a cost-effective solution for creating complex parts with tight tolerances and excellent surface finishes.
If you're ready to explore the benefits of die casting for your next project, CADmore provides top-notch design and engineering services tailored to your specific needs. Contact us today for a quote on your die casting project.