Selective Laser Sintering (SLS) is a powerful and versatile 3D printing technology that has revolutionized various industries by enabling the creation of complex, durable, and functional parts directly from digital designs. In this blog, we will delve deep into the world of SLS, exploring its process, the materials it uses, its wide-ranging applications, and the mechanical properties of the parts it produces. By the end, you'll thoroughly understand why SLS is one of the most prominent additive manufacturing technologies today.
What is SLS 3D Printing?
Selective Laser Sintering (SLS) is an additive manufacturing technology that uses a high-powered laser to fuse small particles of powder—typically polymers, metals, and composites—into a solid structure. The process is layer-by-layer, where each layer of powder is selectively sintered according to the cross-sectional geometry of the CAD model, eventually building up the entire part.
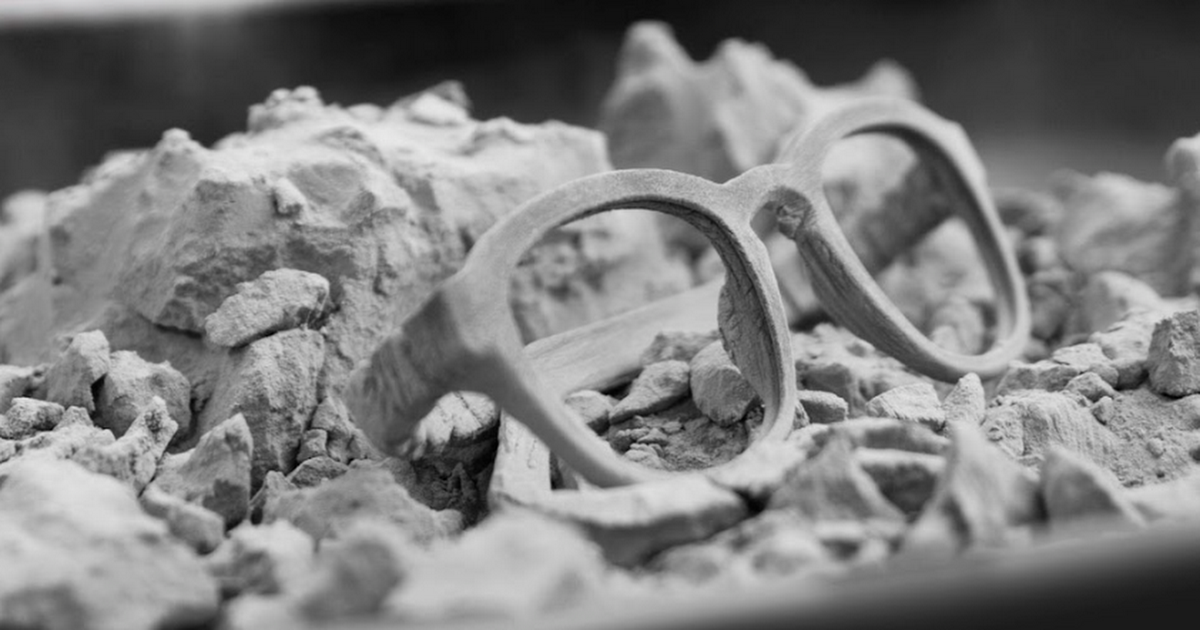
The key advantage of SLS is its ability to produce parts with complex geometries without support structures, unlike other 3D printing methods like Fused Deposition Modeling (FDM) and Stereolithography (SLA). This makes SLS particularly well-suited for creating intricate, interlocking components and parts with internal features that would be impossible to achieve through traditional manufacturing methods.
The SLS Process: How It Works
The SLS process begins with a 3D CAD model of the part, which is digitally sliced into thin layers. The SLS machine spreads a thin layer of powder across the build platform. A laser then selectively sinters the powder, solidifying the material according to the cross-sectional outline of the part. This process repeats layer by layer until the entire part is formed.
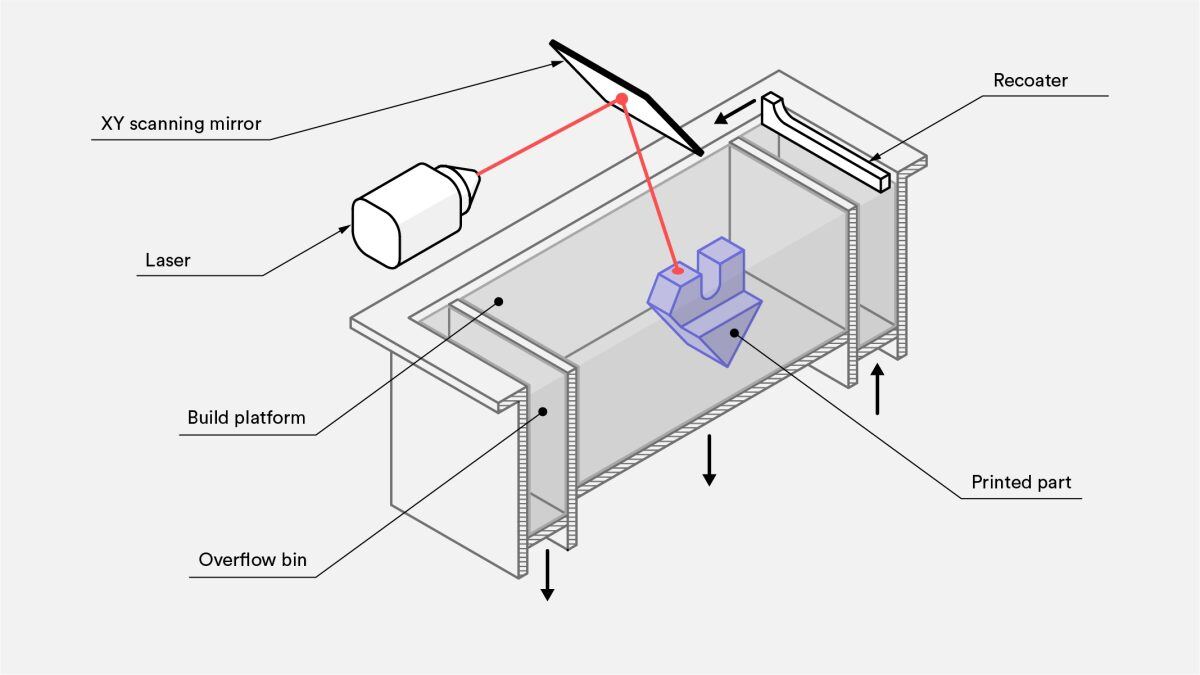
A critical aspect of SLS is the environment within the build chamber. It is typically heated to just below the material's melting point, reducing the amount of laser energy required to sinter the powder. This controlled environment also helps to minimize thermal stresses, resulting in parts with excellent mechanical properties.
Materials Used in SLS 3D Printing
SLS is compatible with various materials, each offering unique properties that make them suitable for various applications. The most commonly used materials in SLS are:
- Nylon (Polyamide): Nylon, particularly PA11 and PA12, is the most popular material used in SLS. It is known for its excellent mechanical properties, high strength, flexibility, and chemical resistance. PA12, for instance, is favored for its balance of toughness and durability, making it ideal for both functional prototypes and end-use parts.
- Metal Powders: SLS can also process metal powders, such as stainless steel, titanium, and aluminum, allowing for the creation of high-strength, heat-resistant components. Titanium Ti6Al4V, for example, is commonly used in aerospace and medical applications due to its light weight, corrosion resistance, and biocompatibility(material_datasheet_eos_…).
- Composites: SLS supports composite materials, such as carbon fiber-reinforced nylon, which offer enhanced mechanical properties like increased strength-to-weight ratio and improved thermal stability. These materials are often used in aerospace and automotive applications where performance is critical.
- Specialty Polymers: SLS can process specialty polymers like PEEK or polycarbonate for applications requiring specific properties, such as flame retardancy or high thermal resistance. These materials are increasingly used in aerospace, automotive, and medical devices.
Applications of SLS 3D Printing
SLS has a broad range of applications across various industries due to its ability to produce parts with complex geometries, excellent mechanical properties, and high durability.
1. Aerospace Industry
The demand for lightweight, strong, and heat-resistant components is ever-present in aerospace. SLS manufactures parts such as ductwork, brackets, and even complex assemblies like fuel nozzles. The ability to produce parts with intricate geometries without additional tooling makes SLS ideal for aerospace applications. Furthermore, using materials like titanium in SLS printing allows for parts that meet the stringent requirements of the aerospace industry (Metal 3D Printing Achieves Lightweight Manufacturing in Aerospace Industry)(Metal 3D Printing Reduces Manufacturing Costs in Aerospace Industry).
2. Automotive Industry
The automotive industry benefits from SLS by using it for both prototyping and low-volume production. Complex components such as intake manifolds, custom interior parts, and even fully functional prototypes are often produced using SLS. The ability to iterate quickly on designs without the need for expensive molds or tooling significantly reduces development time and cost.
3. Medical Industry
SLS is increasingly used in the medical field to create custom implants, prosthetics, and surgical guides. The technology’s ability to produce biocompatible materials like nylon and titanium makes it suitable for patient-specific devices that are both durable and safe for medical use. SLS allows for rapidly producing customized implants that perfectly fit the patient’s anatomy, improving outcomes and reducing surgery time (What is Cold Metal Fusion).
4. Consumer Goods
In the consumer goods sector, SLS is used to create everything from custom eyewear to intricate jewelry designs. The technology’s ability to produce complex, lightweight, and durable parts allows designers to push the boundaries of what is possible, leading to innovative products that stand out in the market.
Mechanical Properties of SLS-Printed Parts
The mechanical properties of parts produced using SLS are among the best in additive manufacturing, making it a preferred choice for functional prototyping and end-use parts.
1. Tensile Strength
SLS parts, especially those made from nylon or metal powders, exhibit excellent tensile strength, making them suitable for applications that require durable, load-bearing components. For example, SLS-printed nylon PA12 typically has a tensile strength of around 48 MPa, comparable to injection-molded parts.
2. Flexibility
The flexibility of SLS materials, particularly polymers like nylon, is another key advantage. Parts made from nylon PA11 or PA12 can flex without breaking, making them ideal for applications requiring impact resistance or elasticity. This flexibility also allows for creating snap-fit joints and other complex mechanical assemblies.
3. Durability
SLS parts are known for their durability, particularly in harsh environments. Materials like nylon and titanium provide excellent resistance to wear, impact, and chemical exposure, ensuring that parts remain functional over long periods and under demanding conditions. This durability is especially important in industries like automotive and aerospace, where parts must withstand extreme conditions.
4. Thermal Stability
One of the standout properties of SLS-printed parts is their thermal stability. Materials like polycarbonate and PEEK, which can be processed using SLS, offer high heat resistance, making them suitable for use in high-temperature environments such as under-the-hood automotive components or aerospace engine parts.