In the realm of 3D printing, two technologies that often come under the spotlight for their innovative approaches and diverse application possibilities are HP's Multi Jet Fusion (MJF) and Stratasys's PolyJet. While both technologies have revolutionized the way we think about manufacturing and prototyping, they cater to distinct needs and offer different advantages. Let's delve deeper into these two technologies to understand their core differences and optimal use cases.
Multi Jet Fusion (MJF) Technology: Engineered for Strength
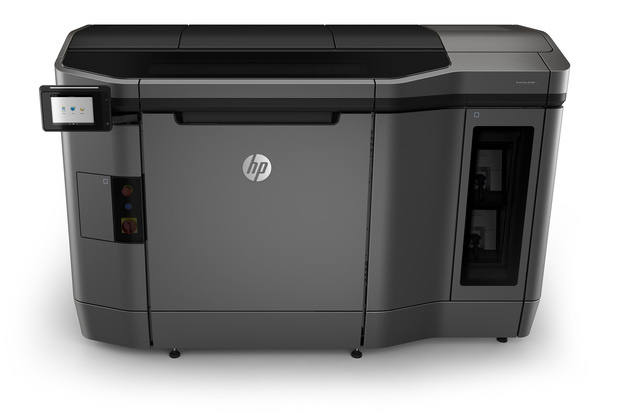
HP's Multi Jet Fusion technology is a powerhouse when it comes to producing strong and durable parts. Ideal for functional applications, MJF utilizes thermoplastic materials that are known for their robustness. This makes MJF an excellent choice for creating parts that are expected to endure stress and wear, such as tools or functional components.
Material Properties: MJF parts are characterized by their mechanical strength and durability, attributes that are critical for components like keys used to open compressor cabinet doors. The thermoplastics used in MJF are engineered to withstand substantial stress, making them suitable for a range of industrial applications.
Printing Process: The MJF process involves laying down a powder material layer, applying detailing agents, and then fusing everything together with heat. This layer-by-layer method allows for the creation of complex geometries with a high degree of precision.
Color Capabilities: While MJF does offer color capabilities, they are typically more limited compared to PolyJet. MJF focuses on grayscale shades, although recent advancements have expanded its color palette, primarily emphasizing functional aspects over aesthetics.
Post-Processing: MJF parts may require some post-processing, such as bead blasting, to achieve a smooth surface finish. However, this technology generally demands less finishing work compared to other 3D printing methods, streamlining the production process.
PolyJet Technology: A Symphony of Colors and Materials
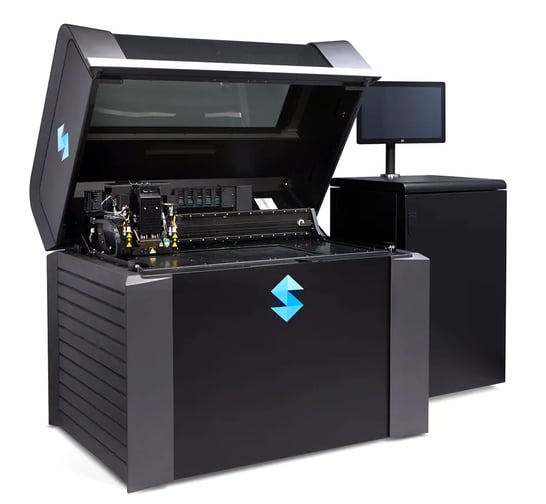
Stratasys's PolyJet technology is akin to an artist's palette, offering a rich array of colors and materials. This technology excels in producing models where aesthetic details and tactile qualities are paramount, making it ideal for prototypes, conceptual models, and presentation pieces.
Material Properties: PolyJet is renowned for its ability to print with multiple materials in a single job, ranging from rigid to flexible. This versatility, however, comes with a trade-off in material durability compared to MJF, positioning PolyJet as a go-to for prototypes and models where form takes precedence over function.
Printing Process: PolyJet employs a photopolymer jetting technique that layers and then cures liquid photopolymer resins using UV light. This process achieves exceptional detail and surface smoothness, allowing for the creation of intricate models with a high level of precision.
Color Capabilities: One of PolyJet's standout features is its full-color printing capability. It can produce parts in a wide spectrum of colors, including transparent materials, enabling the creation of lifelike models that can mimic the appearance and feel of the intended final product.
Post-Processing: Although PolyJet models require cleaning to remove support material, they typically need less manual finishing to achieve the desired aesthetic quality, especially when it comes to color accuracy and material effects.
Practical Applications: A Comparative Look
When deciding between MJF and PolyJet, consider the end use of your printed part. For functional applications where durability is key, such as the keys for compressor cabinet doors, MJF's robust material properties make it the superior choice. In contrast, for the Compressor Station Design (CSD) model intended for presentation, where visual and tactile qualities are crucial, PolyJet's ability to produce high-detail, full-color parts offers a clear advantage.
In summary, while MJF offers unmatched strength and durability for functional parts, PolyJet stands out for its aesthetic versatility and detail accuracy. Understanding these distinctions can help you choose the right technology for your specific project needs, whether you're creating a durable tool or a detailed prototype for presentation.