Leveraging Additive Manufacturing Across the Automotive Manufacturing Process
Additive manufacturing (AM) offers unique benefits at every stage of the automotive manufacturing process, from initial design and prototyping to final production and maintenance, repair, and operations (MRO). By integrating AM, automotive manufacturers can enhance efficiency, reduce costs, and drive innovation.
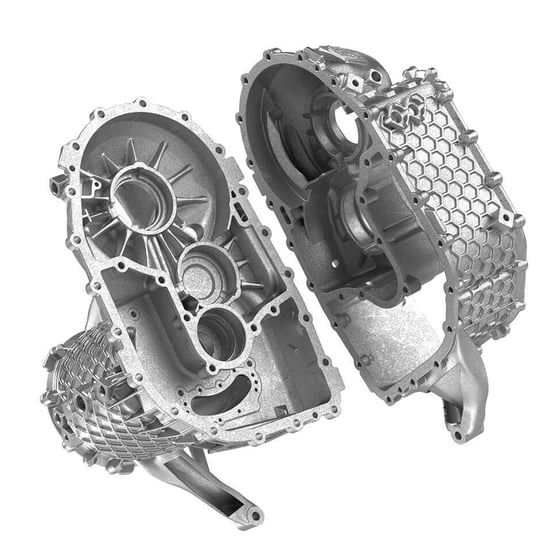
1. Design and Prototyping
Rapid Prototyping: AM allows for the quick creation of prototype parts directly from CAD models, significantly reducing the time and cost associated with traditional prototyping methods. This enables designers and engineers to iterate rapidly, testing multiple versions of a part to optimize performance and functionality. This iterative process leads to better designs and faster development cycles.
Case Example: Ford uses its 3D printing center in Cologne to produce tools and fixtures, accelerating the prototyping process for its first all-electric vehicle built in Europe. This capability allows for rapid adjustments and improvements based on real-world testing, ensuring that designs are optimized before full-scale production begins. Learn more: Ford Opens New 3D Printing Centre.
Design Validation: Functional prototypes created with AM can be tested under real-world conditions to validate design assumptions and identify potential issues before moving to full-scale production. This reduces the risk of costly design changes later in the production cycle and ensures that the final product meets all performance and safety requirements.
2. Tooling and Fixtures
Custom Tooling: AM can produce customized tools and fixtures tailored to specific production needs. This includes jigs, molds, and assembly aids that improve precision and reduce setup times. Custom tooling ensures that manufacturing processes are optimized for efficiency and quality, leading to higher productivity and lower costs.
Case Example: Toyota’s use of Zortrax 3D printers to manufacture assembly jigs and tools has streamlined its production processes, reducing lead times and costs while ensuring high precision and reliability. Producing tools on demand allows Toyota to maintain high operational flexibility and responsiveness.
Flexible Production Aids: By producing tools on demand, AM eliminates the need for extensive inventories of specialized tools. This flexibility allows for quick adjustments to production lines and supports creating customized or limited-run products without extensive retooling. This approach also reduces storage costs and minimizes waste. Learn more: Toyota is using AI and 3D printing as tools.
3. Production and Assembly
End-Use Parts: AM is increasingly used to produce end-use parts directly, especially for low-volume or highly customized components. This capability is particularly valuable for producing complex parts that would be difficult or impossible to manufacture using traditional methods. The ability to produce parts with intricate geometries enhances vehicle performance and aesthetics.
Case Example: Volkswagen is exploring binder jetting technology to produce lightweight structural components for its vehicles. This technology would significantly reduce the weight and cost of parts like the A-pillar in the T-Roc convertible, improving vehicle performance, enhancing fuel efficiency, and reducing emissions.
On-Demand Manufacturing: AM enables on-demand parts production, reducing the need for large inventories and minimizing waste. This approach is beneficial for producing spare parts and components with long lead times or infrequent demand. On-demand manufacturing supports just-in-time production strategies, reducing storage costs and improving supply chain efficiency.
4. Quality Control and Inspection
Custom Gauges and Inspection Tools: AM can produce customized gauges and inspection tools that enhance the precision and efficiency of quality control processes. These tools can be tailored to specific parts and processes, improving the accuracy and speed of inspections. This ensures that all parts meet stringent quality standards before they are assembled into final products.
Case Example: Ford’s 3D printing center in Cologne produces measuring gauges and templates for quality control, ensuring consistent and precise production standards. Custom inspection tools enhance the reliability and repeatability of quality control processes, reducing the risk of defects and rework.
Digital Integration: AM integrates seamlessly with digital design and inspection tools, enabling automated quality control processes and real-time feedback. This integration supports continuous improvement and maintains high-quality standards throughout the production process. Digital integration also facilitates data collection and analysis, driving further improvements in quality and efficiency.
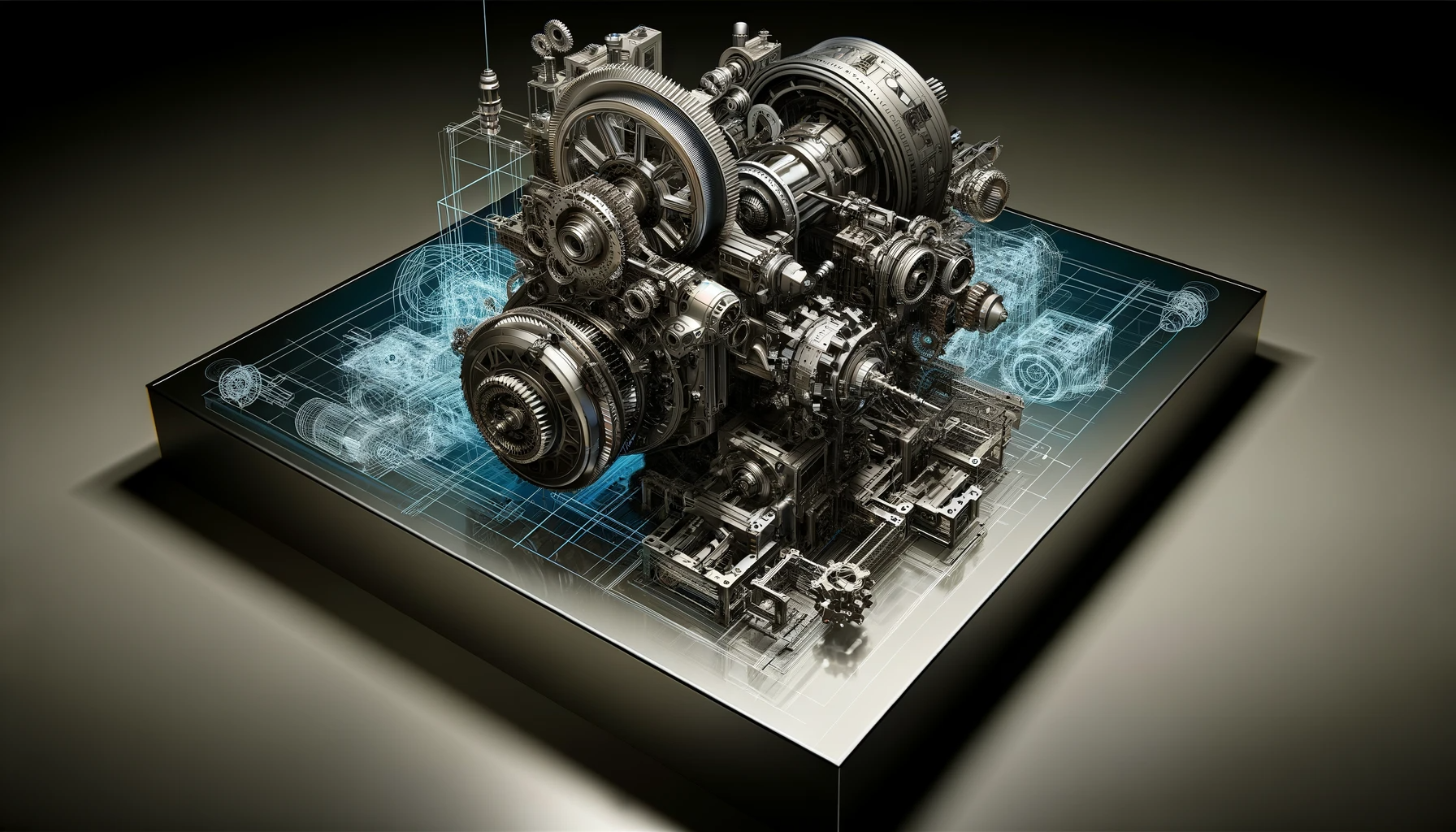
5. Maintenance, Repair, and Overhaul (MRO)
Rapid Replacement Parts: AM provides a solution for producing replacement parts quickly, reducing downtime and maintenance costs. This is especially valuable for older equipment or custom machinery where spare parts may be challenging to source. The ability to produce replacement parts on demand ensures that equipment can be repaired and returned to service quickly, minimizing disruption to operations.
Case Example: At Ford’s Sharonville Transmission Plant, employees use 3D printers to produce replacement parts and fixtures on demand, significantly reducing downtime and maintenance costs. This approach improves operational efficiency and reduces the reliance on external suppliers for spare parts. Read More: Ford is Saving Millions through 3D Printing.
Customized Repair Solutions: AM enables the production of custom repair tools and components specifically designed for the equipment being serviced. This customization improves repair quality and extends the lifespan of machinery. Custom repair solutions can be tailored to address specific wear and damage issues, enhancing the effectiveness of maintenance operations. Example: Toyota Cuts Manufacturing Costs.
Inventory Reduction: By producing parts as needed, AM reduces the need for large spare parts inventories, freeing up storage space and reducing carrying costs. This approach supports a lean inventory strategy and enhances operational efficiency. Reduced inventory levels also decrease the risk of obsolescence and waste. Example: BMW Expands Use of Additive Manufacturing.
Conclusion
Additive manufacturing holds immense potential to transform the automotive industry by offering unparalleled design flexibility, cost efficiency, and production speed. By strategically implementing AM technologies, automotive manufacturers can drive innovation, reduce costs, and enhance their competitive edge. As the technology continues to evolve, its integration into the automotive industry will only deepen, paving the way for more agile, sustainable, and responsive manufacturing practices.
About CADmore
At CADmore, based in Columbia, South Carolina, we are leaders in engineering, design services, and on-demand manufacturing. We are ready to assist anyone in the automotive industry looking to begin or expand their use of additive manufacturing. Our expertise and advanced capabilities can help you leverage the full potential of AM, driving efficiency and innovation across your production processes. Whether you are starting with AM or looking to enhance your existing operations, CADmore supports your journey toward a more advanced and competitive manufacturing future.
For more information on how CADmore can help you implement additive manufacturing, please visit our website or contact us directly. Let us help you transform your automotive manufacturing processes with the power of additive manufacturing.