Exploring the Future of Design: Insights from the "Advanced Design for Additive Manufacturing: A Practical Guide" Webinar
As the Vice President of CADmore, I had the distinct pleasure of participating in the "Advanced Design for Additive Manufacturing: A Practical Guide" webinar during the 2023 Shapeways Manufacturing Week. This event provided a unique platform to share our experiences, insights, and the latest advancements in the field of additive manufacturing. In this article, I'd like to share some key takeaways from the webinar, reflecting on how these insights are shaping the future of design and manufacturing.
The webinar was a convergence of ideas and innovations in additive manufacturing, focusing on enhancing design quality, preventing print failures, and broadening our knowledge horizon. It highlighted our partnership with Shapeways, emphasizing the amalgamation of CADmore's design expertise and Shapeways' manufacturing prowess. The discussion revolved around integrating additive manufacturing into traditional processes, understanding the scenarios best suited for additive manufacturing, and the intricacies involved in design software. We also touched upon the growth and impact of 3D printing across various sectors, including its revolutionary applications in aerospace and medical fields and its role in reducing waste and expediting prototyping.
Enhancing Additive Manufacturing: The CADmore-Shapeways Synergy
Over the past four years, our partnership with Shapeways has been a cornerstone in advancing the field of additive manufacturing. This collaboration has led to the successful execution of diverse projects, ranging from the simplest of designs to the most complex mechanical components. This partnership is not just about combining resources; it's about leveraging each other's strengths to push the boundaries of what's possible in design and manufacturing. Our goal has always been to provide solutions that are not just innovative but also practical and accessible.
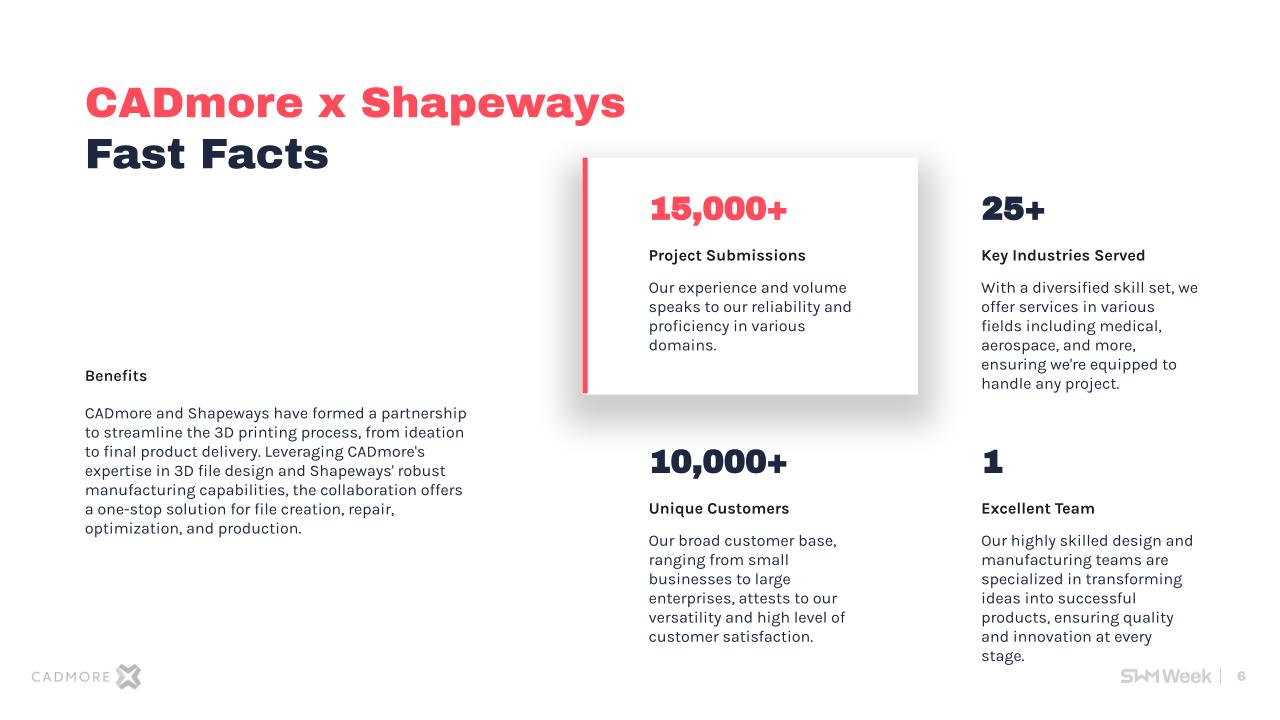
The impact of this collaboration is underscored by our impressive track record: over 15,000 project submissions, reflecting our reliability and proficiency across various domains. Our services span over 25 industries, including the medical and aerospace sectors, showcasing our ability to tackle diverse challenges with a high degree of expertise. Furthermore, our broad customer base, which includes more than 10,000 unique clients ranging from small businesses to large corporations, speaks volumes about our versatility and consistent customer satisfaction.
There’s a lot that comes into play for actually designing something and bringing your concept into real form. That’s why there has been such a huge, and positive, impact in partnering with CADmore, especially due to the massive scope needed for 3D design.
Steve Weart, Director of Customer Success at Shapeways
This partnership isn't just about providing services; it's about setting a new standard in 3D printing by combining creativity with technical excellence, making us a one-stop solution for all 3D printing needs.
Additive Manufacturing: A Growing Force in the Industry
During the webinar, I emphasized the burgeoning role of additive manufacturing in today's industry. With its market expected to soar beyond $35 billion by 2027, it's clear that this technology is more than a passing trend. Its profound impact is evident in sectors like aerospace, where it's used extensively for both prototyping and production. In the medical field, additive manufacturing is creating life-changing solutions, from custom implants to 3D-printed organs. This technology is not just about innovation; it's about making a real difference in people's lives.
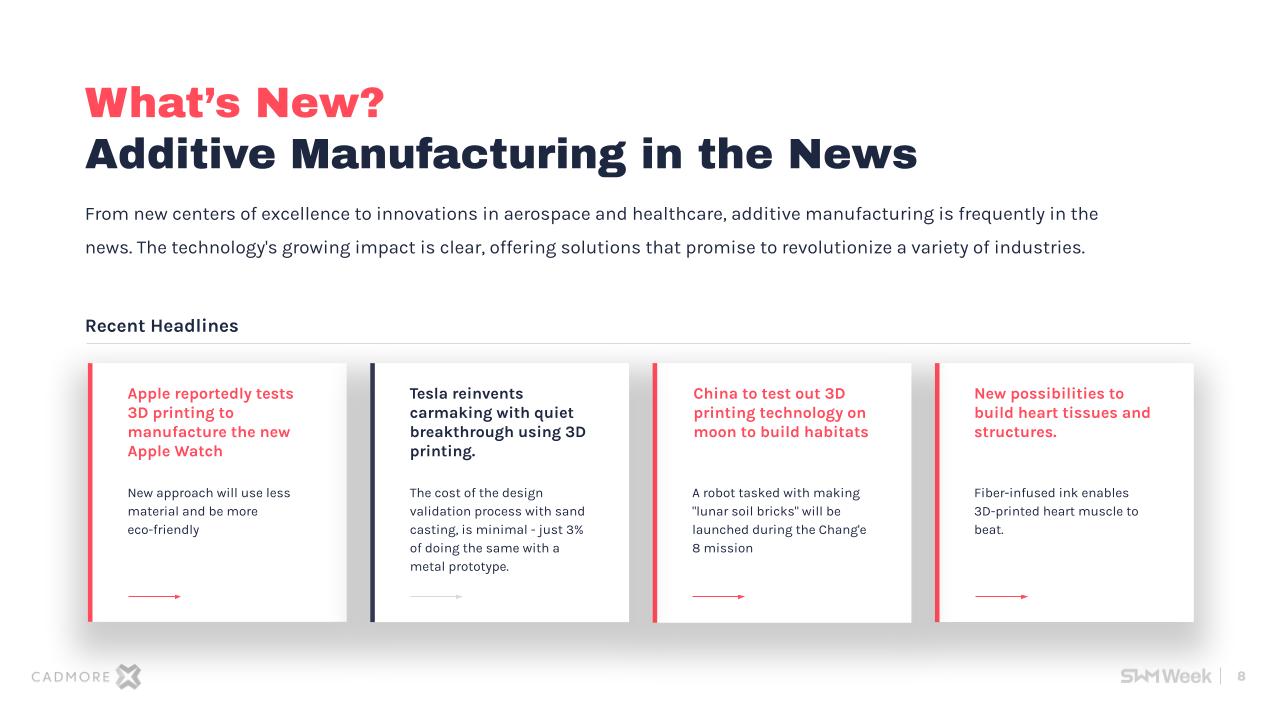
Blending Traditional and Additive Manufacturing
A significant part of our discussion focused on how additive manufacturing complements traditional manufacturing methods. It's a powerful tool for rapid prototyping, creating custom parts, and handling low-volume production with ease. We delved into the specifics of how additive manufacturing can be integrated seamlessly into existing manufacturing workflows, enhancing efficiency and reducing turnaround times.
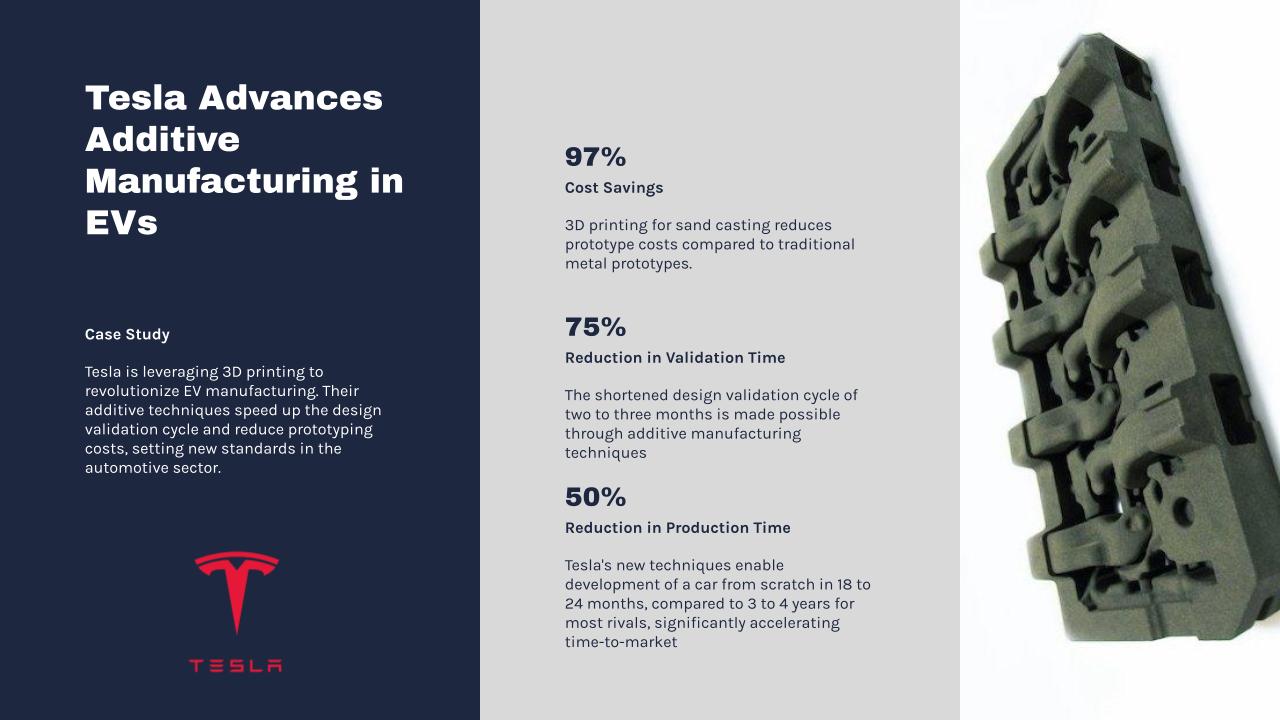
In the realm of additive manufacturing (AM), Tesla's recent innovations offer a compelling case study, particularly relevant to our discussion dyrubg the webinar. Tesla's use of generative design and AM in the Model Y exemplifies the seamless integration of traditional and additive manufacturing methods. The Model Y's rear underbody, initially comprising 70 different parts, was reimagined into just two and eventually a single metal piece, showcasing the incredible potential of AM in reducing part complexity and enhancing manufacturing efficiency.
This approach streamlines the manufacturing process and demonstrates the practical application of AM in large-scale production. Tesla's utilization of 3D printing for sand casts, enabling a drastic reduction in subassemblies, highlights the transformative potential of AM in traditional manufacturing contexts. Such advancements underscore the significant role of AM in automotive manufacturing, where it can support high-throughput production while offering considerable advantages in terms of design flexibility and efficiency.
Mastering Design Software for Additive Manufacturing
Another key aspect we covered was the importance of choosing the right design software for additive manufacturing. The choice between mesh and solid modeling depends on the nature of the project, and understanding this is crucial for achieving optimal results. We also discussed the importance of file optimization and the role of slicing tools in preparing models for printing. These technical details are vital for anyone looking to excel in additive manufacturing.
Utilizing Shapeways' Advanced 3D Tools
Shapeways offers a range of tools that are indispensable in preparing models for 3D printing. These tools, which include mesh integrity checks and guidelines for wall thickness, are essential for ensuring the success of a print job. During the webinar, I highlighted how these tools simplify the preparation process, making 3D printing more accessible and efficient.
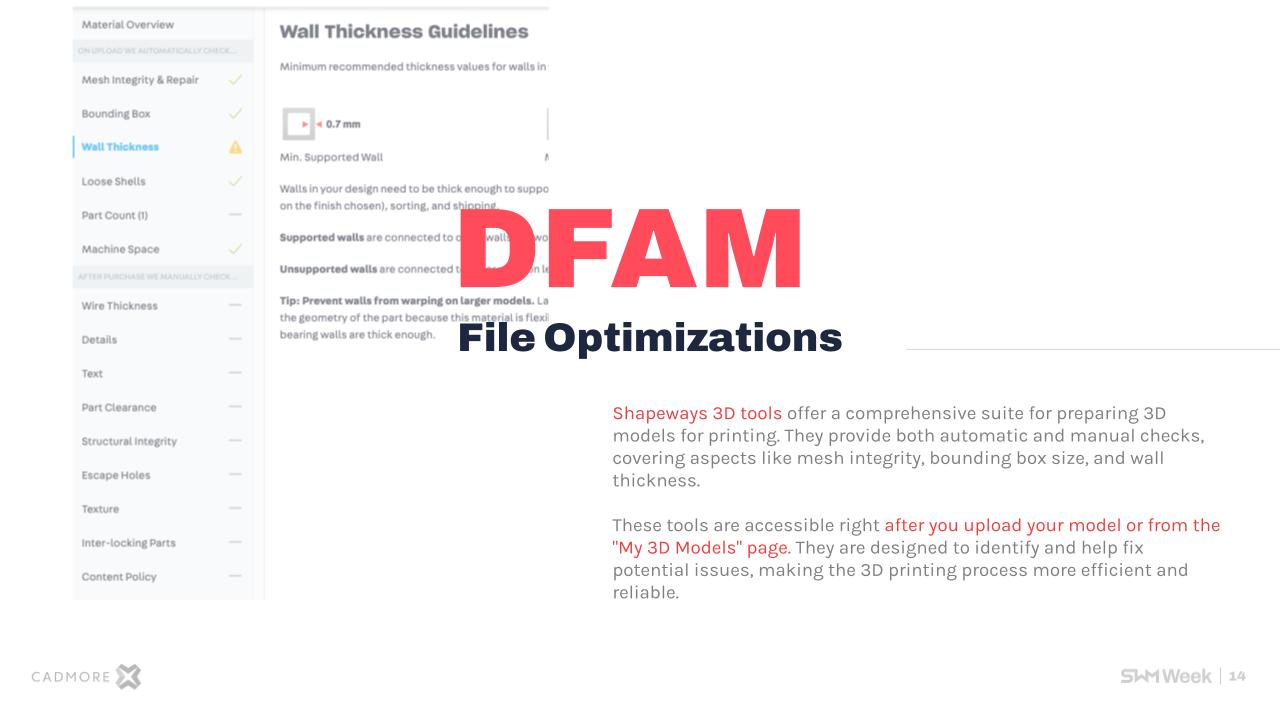
Question and Answer
The world of design is constantly evolving, with new trends and technologies reshaping the way we approach creativity and manufacturing. In this section, I'll address some of the questions from the webinar that help navigate these changes, focusing on 3D modeling, design best practices, and future perspectives.
1. Latest Trends in Design: The current design landscape is characterized by a strong emphasis on sustainability, customization, and digital integration. We are seeing a surge in the use of eco-friendly materials and processes, along with a growing demand for personalized products facilitated by technologies like 3D printing.
2. The Future of Design: I envision a future where design is seamlessly integrated with advanced technologies like AI and augmented reality, leading to more efficient and creative outcomes. The possibilities for innovation are boundless, especially with the advent of smart materials and responsive design techniques.
3. Getting Started with 3D Modeling/Design: For beginners, I recommend starting with user-friendly software like Tinkercad or SketchUp. It's crucial to understand the basic principles of 3D modeling, such as geometric shapes and dimensions, before progressing to more complex software.
4. Contacting for Product Modeling: If you have an idea for a product you need modeled, reaching out to a professional design service like CADmore is a great start. We have experts who can help bring your ideas to life with the right blend of creativity and technical expertise.
5. Best Software for 2D vs. 3D Modeling: For 2D modeling, software like Adobe Illustrator or AutoCAD is widely used. In 3D modeling, Blender, SolidWorks, and Autodesk Fusion 360 are popular choices, each catering to different aspects of 3D design.
6. Resources for Planning a Design: When planning a design, it's essential to consider resources like material guides, design handbooks, and online tutorials. Websites like Instructables, or platforms like LinkedIn Learning offer valuable insights into various design aspects.
7. Protecting Intellectual Property Rights: To protect your intellectual property when sharing files, consider using non-disclosure agreements (NDAs) and ensuring your designs are patented or trademarked.
8. Recommended 3D Modeling Software: I recommend software like SolidWorks or Autodesk Fusion 360 for professional use. For beginners or hobbyists, Blender or Tinkercad can be great starting points.
9. Accepted File Formats for 3D Models: We typically accept file formats such as STL, OBJ, and STEP, which are widely used and compatible with most 3D printing and manufacturing processes.
10. Preparing 3D Models for Printing or Manufacturing: Best practices include ensuring the model is watertight, optimizing the orientation for printing, and considering the material and printing technology to be used.
11. Ensuring Compatibility with Software: To ensure your 3D models are compatible with our software, stick to commonly used formats like STL or OBJ, and check the software specifications beforehand.
12. Troubleshooting 3D Printing Problems: Common tips include checking the printer's calibration, ensuring the material is suitable for the design, and revisiting the slicing settings if issues arise.
13. Preparing 2D Drawings for Printing or Manufacturing: Ensure accuracy in dimensions, use standard drawing conventions, and provide comprehensive details for materials and finishes.
14. Design Guidelines to Follow: Adhere to guidelines related to material selection, minimum feature sizes, and tolerances specific to your manufacturing process.
15. Addressing Cost and Budget Constraints: When designing, consider the cost of materials, manufacturing processes, and the complexity of the design to stay within budget.
16. Favorite Design Tools and Resources: I often use CAD software forums, online design communities, and industry publications to stay updated and get inspiration.
17. Tips for Improving Design Workflow: Streamlining your workflow can involve using software shortcuts, organizing your files efficiently, and continuously learning new techniques and tools.