In architecture, engineering, and construction (AEC) professionals often rely on Navisworks, a powerful tool from Autodesk, to streamline project coordination, clash detection, and 3D design review. However, while Navisworks is effective for visualizing and managing complex models, it’s important to understand its limitations—especially when it comes to file conversion.
Navisworks excels as a viewer and reviewer of 3D models but falls short when used as a source for converting files into other formats. Many users mistakenly attempt to convert Navisworks files like NWD, NWF, or NWC into CAD formats, only to encounter issues with data loss and reduced precision. The reality is that Navisworks was never intended to be a conversion tool, and forcing it into this role can lead to significant challenges.
This blog will explore why converting Navisworks files is generally a bad idea, explain the fundamental differences between mesh and NURBS models, and provide a step-by-step guide for those times when you have no choice but to proceed with a conversion. Ultimately, the best practice is to avoid this route altogether and instead go back to the original CAD files whenever possible. Here’s why.
Why You Should Avoid Converting Navisworks Files Directly
Navisworks is primarily a mesh-based program, using polygon models to represent 3D objects. These mesh models are excellent for visualization and coordination but lack the precision and scalability of NURBS (Non-Uniform Rational B-Splines) or solids-based models used in CAD software. When you attempt to convert these mesh-based files into CAD formats such as STEP or IGES, you’re likely to encounter significant issues, including loss of detail and accuracy.
In most cases, if you have an NWD file, your MCAD (Mechanical Computer-Aided Design) data originally came from a more suitable source, such as Intergraph PDS, Microstation DGN, or AVEVA PDMS. Navisworks is intended to serve as an intermediate viewer, not as a source of precise engineering data. Using it for file conversion often leads to a degradation of data quality through multiple format changes—like going from the original software to Navisworks, from Navisworks to FBX, and finally from FBX to STL. This process introduces errors and reduces the overall fidelity of the model.
Mesh vs. NURBS: Understanding the Difference
To fully appreciate why converting Navisworks files can be problematic, it’s essential to understand the difference between mesh and NURBS models. Mesh models, which are used in Navisworks, consist of thousands or even millions of small triangles. These triangles define the surface of the model but are prone to losing detail during scaling or conversion.
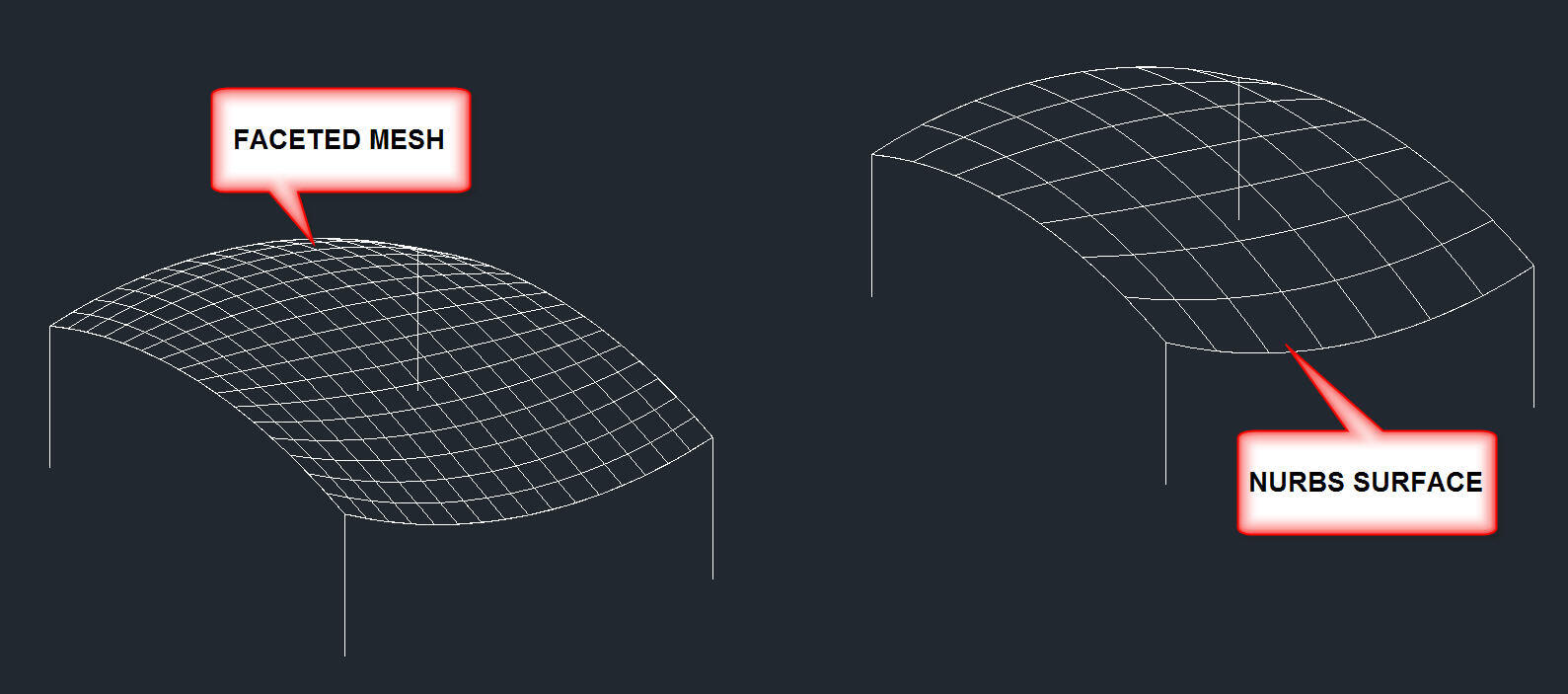
On the other hand, NURBS models are defined by mathematically precise curves, making them infinitely scalable without any loss of detail. This precision is critical in CAD applications where accurate measurements and complex geometries are required. Converting a mesh model to a NURBS model—a process known as reverse engineering—is complex and often results in a model that lacks the original detail and precision. Read more: https://cadmore.com/blog/solid-vs-mesh-modeling-differences
The Right Way to Handle Navisworks Files
Given these challenges, the best approach is to avoid converting Navisworks files whenever possible. Instead, trace the data back to its original CAD source. This ensures you retain the full precision and detail of the model, which is crucial for any subsequent engineering or manufacturing processes.
However, if you must work with a Navisworks file and no other options are available, there are ways to convert it, albeit with caution. For instance, you can export the Navisworks file to FBX format first. This format is more widely supported by other software, and you can then import the FBX into most CAD programs and export it further into formats like STL. Keep in mind that each conversion step will lead to a loss of precision, making this approach a last resort rather than a preferred metho.
Step-by-Step Guide to Exporting from Navisworks
- Export to FBX: Open your Navisworks file in Navisworks Simulate or Manage. From there, export the file to the FBX format. This step is crucial because FBX is one of the few formats that can bridge the gap between Navisworks and other CAD software.
- Import FBX into CAD Software: Once you have the FBX file, import it into a CAD program that supports FBX, such as Autodesk 3ds Max or Blender.
- Export to STL or Other Formats: After importing the FBX file, you can export it to an STL or other formats as needed. Be aware that the model may lose detail during this conversion, especially if it contains complex geometries.
- Review and Adjust: After conversion, carefully review the model for any inaccuracies or loss of detail. You may need to make manual adjustments to restore some of the precision lost during conversion.
Conclusion
Converting Navisworks files directly is generally not recommended due to the inherent limitations of mesh-based models and the potential loss of precision during conversion. Whenever possible, it's better to go back to the original CAD files to ensure that you retain the full integrity and accuracy of your models. However, if you're left with no other choice, the outlined process can help you navigate through the conversion with the understanding that the final output may not meet the exact standards of the original data.
By following these guidelines, you can make informed decisions about when and how to convert Navisworks files, minimizing the risk of data loss and ensuring that your final products maintain the quality and precision required for your projects.