Cold Metal Fusion
Process-Overview
Cold Metal Fusion prints a “green” part on a low‑cost plastic SLS machine by lightly fusing a metal‑powder and polymer‑binder mix; the loose powder is removed and reused, and the green part—already stiff enough to mill or drill—can be machined before it ever hardens. The part then sits in a solvent bath that dissolves most of the binder, after which a furnace slowly ramps to the alloy’s sintering temperature: the last 1–3 % binder burns off, metal particles fuse, and the part shrinks uniformly to about 97–99 % density. Optional finishing steps such as blasting, polishing, heat treatment, or hot isostatic pressing bring the part to final surface and mechanical specifications.
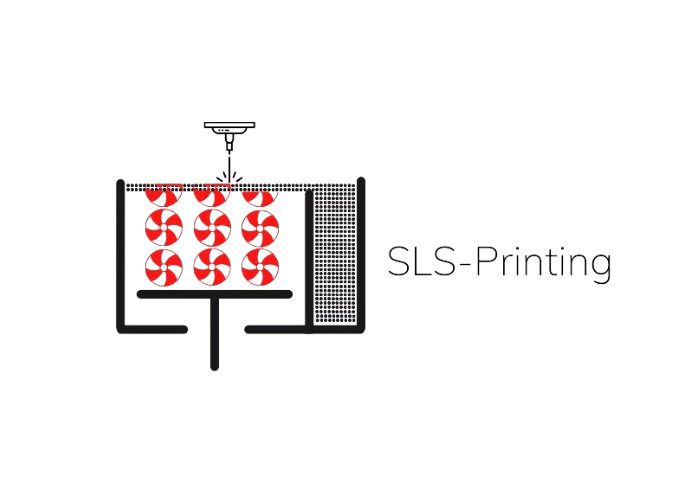
SLS-Printing
Uses inexpensive, widely available plastic SLS hardware; full build volume can be packed tightly.
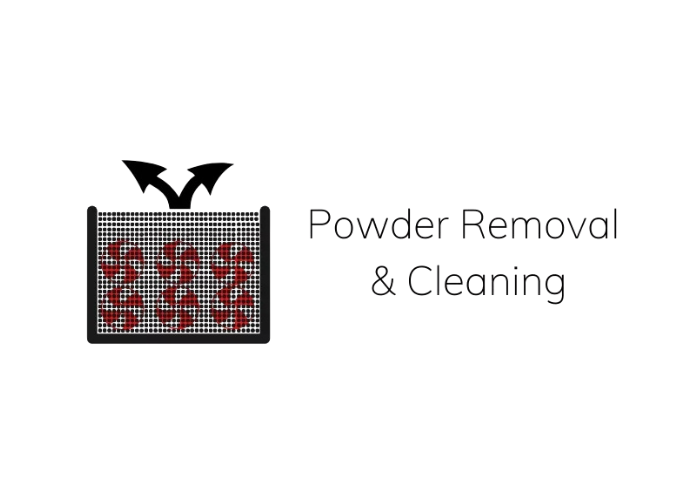
Powder removal & cleaning
Fast, automated depowdering keeps material costs low and waste near zero.
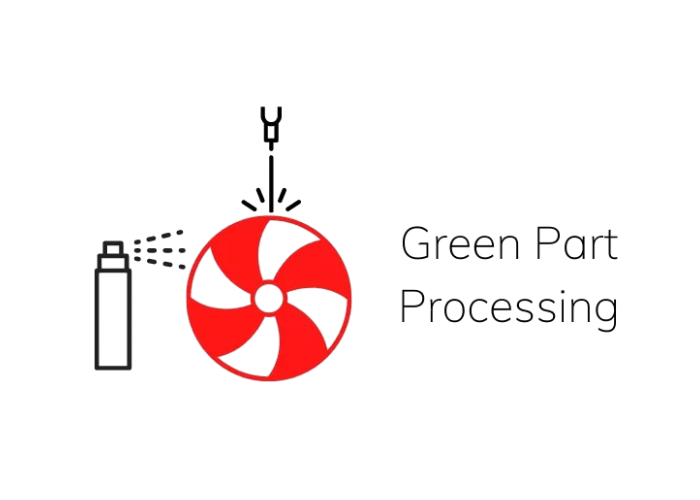
Green-part processing
Let's you add features, improve tolerances, or remove excess stock while the material is still soft and tool-friendly.
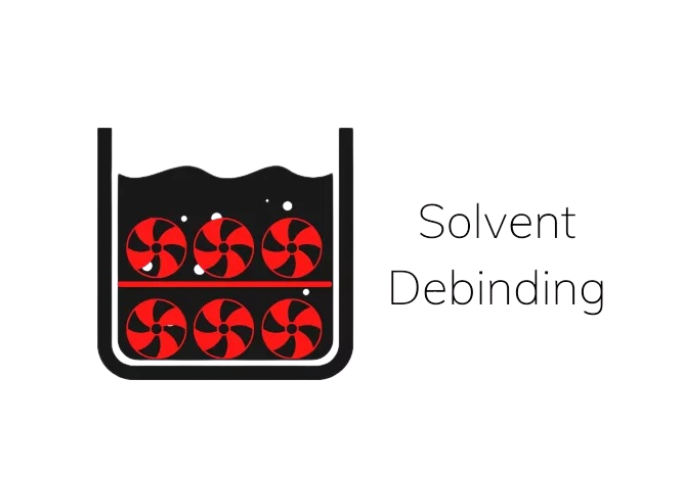
Solvent debinding
Cheap, scalable, and environmentally friendlier than thermal debinding alone.
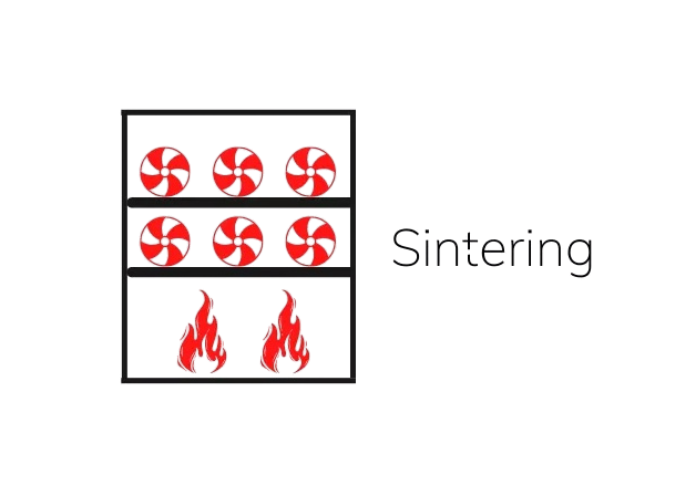
Sintering
Produces a fully metallic, near-wrought part with consistent shrink and excellent mechanical properties.
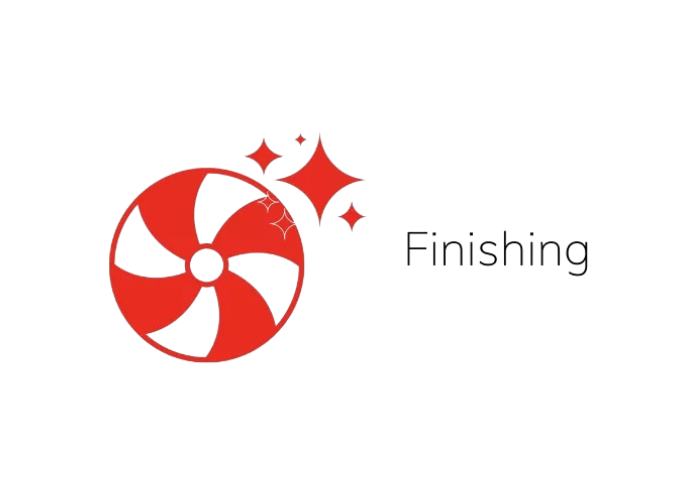
Finishing (optional)
Tailors surface roughness, micro‑structure, and density to the application.
Cold Metal Fusion (CMF) in six quick steps
-
SLS-Printing
A standard polymer-laser-sintering (SLS) machine spreads a metal-powder plus plastic-binder mix and lightly melts the binder (<80°C). Layers build up with no support structures.
-
Powder removal & cleaning
The cooled "cake" is blown out or water-jetted. Unsintered powder is collected and reused.
-
Green-part processing
The printed-green parts are strong enough for turning, milling, drilling, or grinding before they ever see a furnace.
-
Solvent debinding
Parts soak in a temperature-controlled solvent that dissolves a portion of the binder; the solvent is distilled and reused.
-
Sintering
Furnace ramps to metal-specific temperature; remaining 1-3% binder burns off, metal particles fuse, and the part shrinks uniformly (≈13% for 316L). Final density: 97-99%.
-
Finishing (optional)
Surface treatments: grinding, polishing, blasting, anodizing, heat treatment, or HIP to reach final spec.